What are the causes of static electricity in manufacturing?
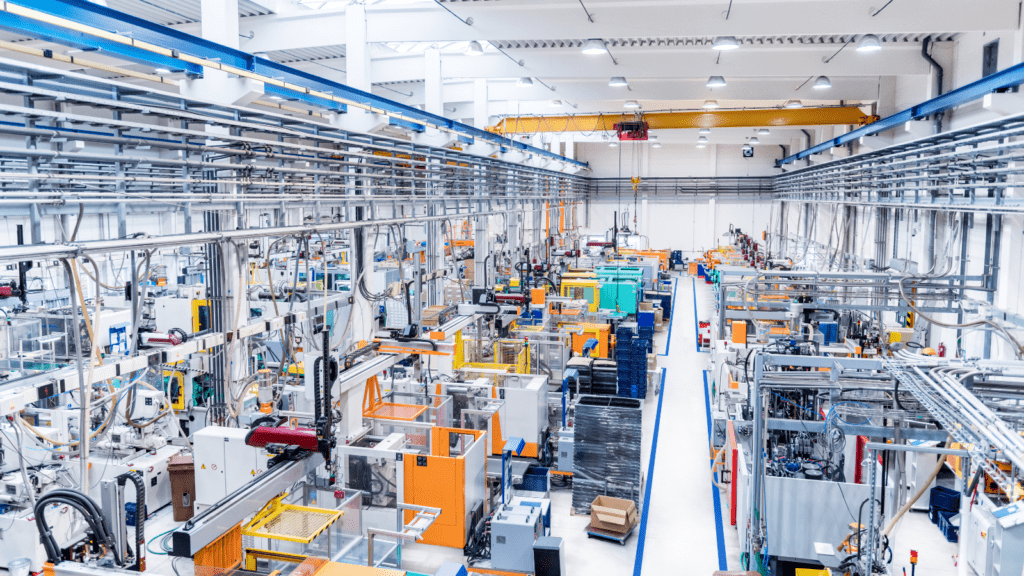
Static electricity can be a significant concern in manufacturing processes as it can lead to various issues, including safety hazards, product defects, and equipment damage. Several factors can cause static electricity to build up in manufacturing environments:
- Friction: One of the primary causes of static electricity in manufacturing is friction between materials. When two materials rub against each other or are separated after being in contact (triboelectric effect), electrons can be transferred from one material to another, leading to a charge imbalance.
- Material Properties: The electrical conductivity or resistivity of materials plays a crucial role in static electricity generation. Materials that are poor conductors of electricity, such as plastics, insulating rubber, and dry powders, are more likely to build up static charges.
- Relative Humidity: Low humidity levels can exacerbate static electricity issues. Dry air provides fewer opportunities for charges to dissipate, allowing static electricity to accumulate more readily. Controlling humidity in manufacturing environments can help mitigate static electricity problems.
- Material Movement: The movement of materials on conveyors, through pipes, or during manufacturing processes can cause static charges to accumulate. For example, the flow of granular materials or powders through pipes can generate static electricity.
- Non-Conductive Shoes and Flooring: In areas where employees wear non-conductive shoes or work on insulating flooring materials, static charges can build up as they walk or move around.
- Chemical Reactions: Certain chemical reactions can generate static charges as a byproduct. For instance, the mixing of chemicals or the transfer of liquids can lead to static electricity generation.
- Machine Operations: Manufacturing machinery and equipment can generate static electricity as they operate. The movement of belts, rollers, and other mechanical components can create friction and charge imbalances.
- Packaging and Handling: Static electricity can be generated during the packaging and handling of materials, especially if they involve materials like plastic films, foils, or shrink-wrapping.
- Dust and Particles: Dust and fine particles in the air can carry static charges. In environments with a high concentration of dust or airborne particles, static electricity can become a significant issue.
- Insulating Materials: The use of insulating materials or coatings on equipment and surfaces can promote the accumulation of static charges, as these materials inhibit the dissipation of electric charges.
To manage static electricity in manufacturing settings various measures can be employed, such as grounding equipment, using anti-static materials, implementing ionization systems, maintaining appropriate humidity levels and providing static dissipative clothing and footwear for workers. Effective static control is essential to prevent electrostatic discharge-related problems, product defects, and safety hazards in manufacturing processes.
As always, please get in touch if you have any questions and we will try to help.